Polished Stone Value - Test Procedures and Equipment
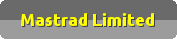 
PSV - Polished Stone Value
Test Procedures and Equipment
Introduction
In 1950 increased traffic flows and higher speeds on trunk roads, together with
concerns about road safety led to research into the relationship between road
materials and skid-resistance.
Research at the UK Road Research Laboratory showed a significant relationship
between polishing of aggregates used in road surfaces and skid resistance. Tests were
devised using an Accelerated Polishing Machine and a friction measuring device, a Skid-
Tester, to determine a Polished Stone Value.
These developments have resulted in a simple and inexpensive procedure to
determine in advance of a road being built what its resistance to skidding will be.
Our Accelerated Polishing Machine was first made 25 years ago, and we
were deeply involved both in the development in the machine and of the test procedures
based on it. More than 1000 of these machines have been supplied throughout the world
to Materials Laboratories, Consulting Engineers and Research Institutions.
The Skid Tester was first made to a design of the UK Road Research Laboratory.
We now offer this machine. Customers may now purchase the two machines required to carry out PSV calculations from the same company, which is also able to provide a full range of spares and technical advice and support.
Calculation of Polished Stone Value
The Polished Stone Value of aggregate gives a measure of resistance to the polishing action
of vehicle tyres under conditions similar to those occurring on the surface of a road.
The action of road vehicle tyres on road surfaces results in polishing of the top, exposed aggregate surface, and its state of polish is one of the main factors affecting the resistance to skidding.
Resistance to this polishing action is determined principally by the inherent qualities of the
aggregate itself. A later section of this memorandum gives some information about the polishing resistant qualities of different sources of aggregate.
The actual relationship between PSV and skidding resistance wilI vary with traffic conditions,type of surfacing and other factors. All factors together with reproducibility of the test should
be taken into account when drawing up specifications for road works which include test limits
for PSV.
The PSV test is carried out in two stages - accelerated polishing of test specimens followed by
measurement of their state of polish by a friction test.
Description of the PSV Test
Full details are given in BS812Part1 14:1989. A copy of this document is essential to
understand and carry out the test.
Four curved test specimens are prepared from each sample undergoing test. Each consists of 35 to 50 representative chippings of carefully controlled size supported in a rigid matrix.
Fourteen specimens are clamped around the periphery of the 'road wheel' and subjected to
two phases of polishing by wheels with rubber tyres. The first phase is of abrasion by a corn
emery for three hours, followed by three hours of polishing with an emery flour. Two of the
fourteen samples are of Control stone.
The degree of polish of the specimens is then measured by means of the portable
skid resistance tester (using a special narrow slider, shorter test length and supplementary scale)
under carefully controlled conditions. Control specimens are used to condition and check the
slider before the test; also a pair of control specimens is included in each test run of fourteen
specimens to check the entire procedure and to allow for adjustment of the result to
compensate for minor variations in the polishing and or friction testing. Results are expressed as
'polished stone values' (PSVs), the mean of the four test specimens of each aggregate.
International Use of the PSV Test - BS 812
This British Standard has been adopted and used widely throughout the world. It is the only test with available equipment to calculate PSVs.
The Permanent International Association of Road Congresses PIARC in conjunction with RILEM and the American Society for Testing Materials (ASTM), recommend the use of BS 812 to determine Polish Stone Values.
Use of PSV in Road Construction Contracts
In the UK the Highways Agency specify PSV tests in circumstances where resistance to polishing have been found to be important. Table 2 shows the values required for various conditions
The machine consists of a road wheel, rotating at 320 rpm, to the periphery of which are
clamped 14 specimen holders. A solid rubber tyred wheel is positioned vertically above the road
wheel, and loaded to exert a force of 725 N.
There are two feed mechanisms and a water supply.
The first mechanism feeds corn emery, mixed with water to the junction of the rubber and
road wheel, while the second mechanism feeds emery flour, with water, to the same
location.
Road Safety and PSV
The fundamental purpose of the PSV is to enable safer roads to be built.
In the UK use of PSVs in road construction has had a major influence in reduction of
accidents. The following is an interesting example.
Elevated section of M4 experiment
This site, the elevated part of Motorway M4, was found to have a high proportion of skidding
accidents when wet. Examination of the records showed that the SFC (Sideways Force
Coefficient) of the surface was from 0.35 to 0.45 at 50 km/h. The road was resurfaced with
the highest PSV material available at the time. It had been intended to use calcined bauxite
(RASC Grade) for the entire site, but as insufficient material was available, it was decided to
mix it with a gritstone from Gilfach quarry near Neath, in South Wales, with a PSV of 71.
During the first three years after resurfacing the SFC was found to have increased to
between 0.50 and 0.60 and accidents were substantially reduced.
TABLE 1
Petrology and Polishing
Extensive research has shown it is not possible to predict polishing qualities of natural
roadstone from petrological data. However some indicators have emerged:
Rocks composed of minerals of widely different hardness, and rocks that wear by the pulling
out of mineral grains from a relatively soft matrix, had relatively high resistance to polishing.
Conversely rocks consisting of minerals having nearly the same hardness wore uniformly and
tended to have a low resistance to polishing.
The gritstone group is excellent, with resistance to polishing being always high, whereas the
lime stone and flint groups yield the lowest resistance. Other groups, basalt, granite and
quartzite, yield intermediate results.
Resistance to polishing of samples from the basalt group show a wide range. Resistance is
higher when minerals of different hardness are present, and when the ground-mass is foliated
or fluxioned. The resistance is also influenced by the proportion and hardness of secondary
minerals, softer minerals giving higher resistance.
In groups of igneous rocks the petrological characteristics which most readily affect
resistance to polishing are variation in hardness between the minerals and the proportion of soft
minerals. Rocks with cracks and fractured minerals are of higher resistance, whereas finer-
grained allotriomorphic rocks tend to polish more readily.
Types of Polishing and Control Material
Four types of material are used in equipment for calculating PSVs.
Emery Corn
The first three hours of the polishing operation uses this material to remove high spots, and
condition the surface of the specimen.
Emery Flour
The second three hours of the polishing operation uses this material to polish the samples.
Control Stone
This stone is used in the polishing Machine to provide a comparison against which the
results of the aggregate under test can be measured. 2 out of 14 samples in each test are
from this material.
Criggion Stone
Used in the Skid Tester for calibration purposes.
The machine is based on the hod principle. It has a pendulum consisting of a tubular arm
rotating about a spindle attached to a vertical pillar. at the end of the tubular arm is a head of
constant mass with a spring loaded rubber slider. The pendulum is released from a horizontal
position so that it strikes the sample of aggregate with a constant velocity. The distance the
head travels after striking the sample is determined by the friction of the surface of the sample,
which has undergone preparation by the Accelerated Polishing Machine.
The results shown by the Skid-Tester as Polished-Stone Values are the coefficient of
friction multiplied by 100.
The Skid-Tester is calibrated by the use of Criggion Stone, which comes from a quarry in
North Wales and is acknowledged to be a material of exceptionally consistent characteristics.
Other Uses of the Skid Tester
Apart from it's key role in calculating Polished Stone Values in a laboratory environment, the
Skid Tester is a principal instrument for testing existing roads, and is an inexpensive alternative
to special purpose vehicles. In developing countries the use of a Skid Tester usually precedes
the purchase and use of an Accelerated Polishing Machine.
Investigations of causes of road accidents often include a Skid Test Report.
The following tests also make use of a Skid Tester:
Polished Paver Value
Polished Mortar Value
Some Other Tests on Aggregates and Surfaces
Aggregate Impact Test
This test is specified in BS812:Part 3 : 1975.
Resistance to impact of a sample of aggregate is measured by subjecting a 28mm deep bed of 14 mm to 10 mm chippings, in a 102mm diameter hardened steel cup, to 15 blows from a 14 kg hammer falling from a height of 380mm. The percentage mass of fines (passing a 2.80mm BS test sieve) formed in the test is known as the aggregate impact value AIV. higher values are given by weaker materials. For the majority of aggregates the impact value and the crushing value are similar, but brittle materials such as flints yield impact values which are about 5 units higher than their crushing values.
The impact test is widely used as an alternative to the crushing test.
Aggregate Abrasion Value
Dorry Abrasion Test
In the original Dorry abrasion test (also known as the Dorry hardness test) the specimens of rock, two in number, each measuring mm in diameter by 25mm long, were pressed against the surface of a cast steel disc, rotating in a horizontal plane, with a force of 25 grams per square centimetre. Crushed quartz was used as an abrasive and was fed in through two small hoppers. The amount of material abraded was measured after 1,000 revolutions of the disc. With minor changes, the test was adopted by the British Standards Institution and incorporated in BS812:1938.Leighton Buzzard sand was used as the abrasive and results were expressed as
the coefficient of hardness (however results were often referred to as abrasion values). The coefficient of hardness being calculated by subtracting from 20,one third of the loss in mass in grams.
The Dorry abrasion test was superseded by the Aggregate Abrasion Test in the 1951
revision of BS 812.
The abrasion machine is similar to that used for the Dorry test and the test was developed in
1949. Resistance to abrasion is measured by finding the percentage loss in mass suffered by 33
cu. cm. of cubical (i.e. neither flaky nor elongated) 14 mm to 10 mm chippings when mounted
in a single flat layer in a suitable setting medium and subjected to a standard abrasion procedure
on a lap using a standard 600 micron to 425 micron Leighton Buzzard silica sand as the
abrasive. The percentage loss in mass of chippings is known as the 'aggregate abrasion value'
(AAV) and ranges from about 1 for hard flints to over 16 for aggregates that would normally
be considered too soft for use in road surfacings.
Inadequate abrasion resistance of road surfacing aggregates means an early loss of the
texture depth required to maintain high speed skidding resistance.
Polished mortar value determination
The procedure is an adaptation of the method and apparatus for measuring the PSV. A sample
of fine aggregate is mixed with ordinary Portland cement to produce a mortar with an
aggregate/cement ratio of 3.0 and a total-water/cement ratio of 0.6. Specimens of the same
size as in the PSV determination are cast so that the upper, screed, surface is subjected to the
polishing cycle. This is basically the same as for the PSV determination except for the omission
of water during the first 3 hour period and minor adjustments to the nominal rate of feed of
both grades of emery. Results are reported as 'polished-mortar values
(Pmvs),.
Polished-paver value determination
The polished paver-value determination makes use of the BS812 aggregate abrasion method to
polish the samples of pavers. the abrasion lap is modified by attaching a standard rubber disk,
and corn emery and emery flour abrasives are fed to the samples under test in the same way
as in the BS812 determination. The specimens are prepared to aggregate abrasion test
specimen dimensions and flat control specimens (of the same control stone as the PSV test)
are also made to these dimensions. After completion of the polishing procedure, the degree of
polish is measured with the portable skid-resistance test in a similar way to the PSV test. A flat
to curved correction factor is then applied to estimate the 'polished-paver value', a correction
being applied in the same way as the PSV test according to the level of the control specimens.
The method has been published by the British Standards Institution a draft for development
(DD 155:1896). It also forms the basis of the draft European Standard - Pr EN 1344 - 1993.
TABLE 2
|